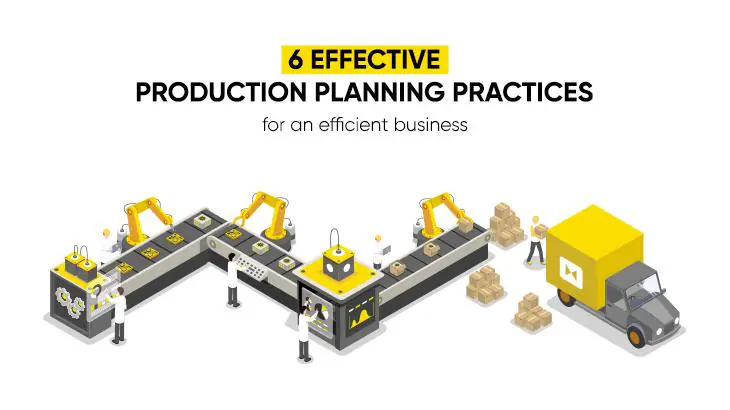
Customer: 90% of the time we face delays in delivery, why?
Production Manager: Next time onwards, it will not happen for sure.
Director of Production Unit (Silently Thinking) : I am also finding out the answer of this “Why”.
Typical Manufacturing Units faces Delivery delay in most of the cases and the best solution that they find across their experience is “Short Term Solution” – Overtime.
Initially, Overtime thrills but it kills the organization in longer run. Employees are unhappy due to giving overtime all the time and customers are unhappy because of delayed delivery. In turn, Companies’ keep their credibility at stake.
Not Only credibility but due to delivery delays, the Organization also faces many challenges :
- Opportunity Loss, New Business
- Customer Loss, Repeat Business
- New Business Loss, Reference from Existing Customer
- Profitability Loss, due to Delay
- Weak Employee Retention, due to Overtime
- High Wastage as an impact of Urgency
- High Cost due to Wastages and Overtime
“The bottleneck is never code or creativity, its lack of clarity”
– Scott Berkun
The ultimate key is to identify the “Culprit of Delivery Delays”. Irrespective of everyone in the value chain meeting the deadline, deliverables are not reaching on time. It means there are some blocks in the process that we need to identify to smooth line the process.
A Best possible route to find the culprit is to start with “Production Planning and Control” which enable companies to track the Production from scratch and map the root cause of delay. It is the tool to coordinate and integrate manufacturing activities. It’s objective is to plan and control all the factors affecting the Production, may be movement of material, labour, machine utilization, any other related activities, outsourcing vendor or any other factor affecting production to meet the deadline.
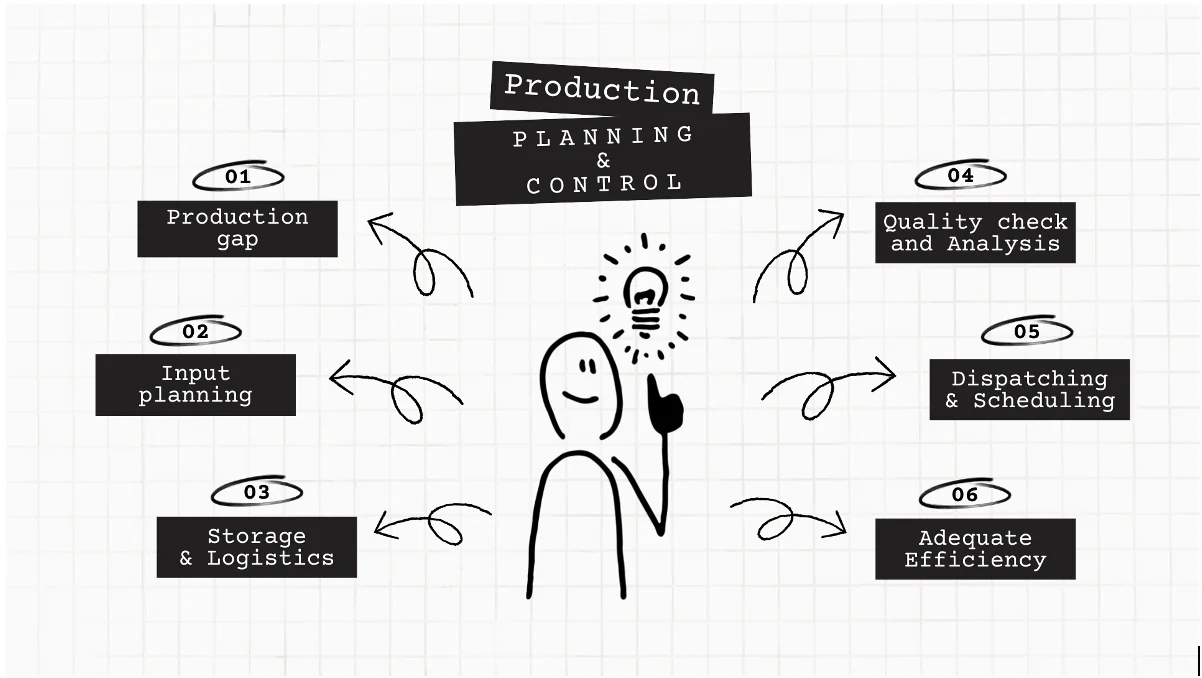
1. A Whole in the Pipeline :
Problem: Before the product reaches the customer it passes through a lot of processes which include multiple machinery processes as well as human resources.
Let’s understand taking one simple example : In one of the Production line, the product passing through 3 processes,
Machine A + Machine B + Machine C = Final Output
If Machine ‘A’ is producing 20 units/hour and Machine ‘B’ is giving an output of 5 units per hour, then it will create stock between the two processes, simultaneously, Process ‘C’ is getting input below its capacity. It ultimately leads to adding extra hours to the final output.
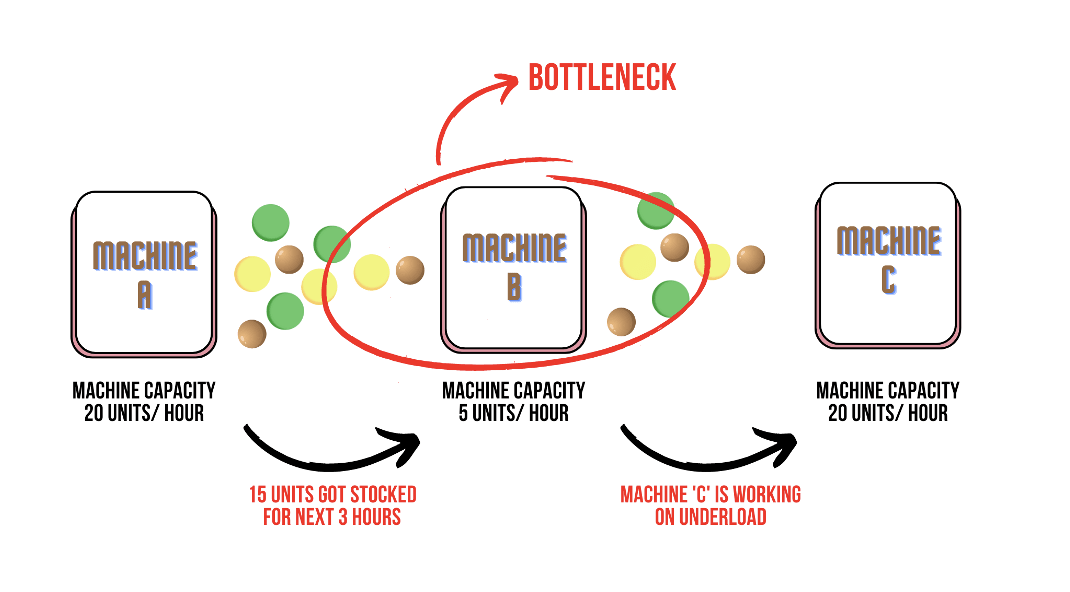
Solution: Line balancing, where if any of the channel/s becomes the bottleneck, increasing the machine at that particular stage of the chain, would help save time, avoid stocking and grab maximum machine utilisation. The purpose of the line balancing is to synchronise the cycle time of each process and avoid the waiting time between the machines.
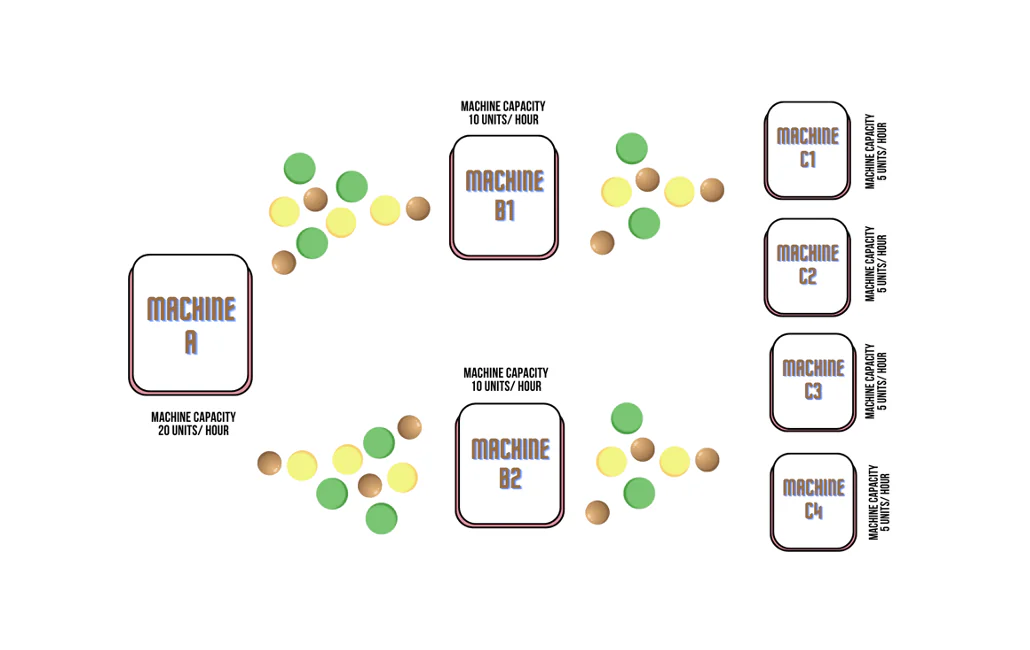
2. Inappropriate Feeding :
Problem: Sometimes, the required inputs are not available at the right time, right place, right quantity and right quality. Additionally, if the last-moment purchase of raw material is made, it cost a premium amount.
Sometimes, the machine’s spare parts are not available at the time of break down stretches the lead time and creates a delay in delivery.
Solution: It can be avoided by adding production planning to the process, involving employees from all levels taking from floor level to the highest management level. In this process creating a ‘Production Report’ helps a lot to track raw materials quantity, machinery performance, Manpower workload & planning, etc before starting the actual production.
Production planning also ensures the selection of the ‘right’ resources – raw material and manpower (skilled/unskilled) for the process to be done correctly or else the struggle in getting right output will remain the same. Additionally, keeping multiple vendors for raw materials is useful in last-minute purchases.
3. Stick to Logistics :
Problem: The availability of finished goods at the time of dispatch is a major issue to address. The arrangements of finished goods that have been produced, is stored in such a way that there is no tracking of what has been produced first and what is new. Above that, the movement of the goods become difficult if it is not trackable.
Solution: Channelized the produced goods and keep track by maintaining reports. Implementing methods like LIFO and FIFO can able to manage the inventory flow accurately.
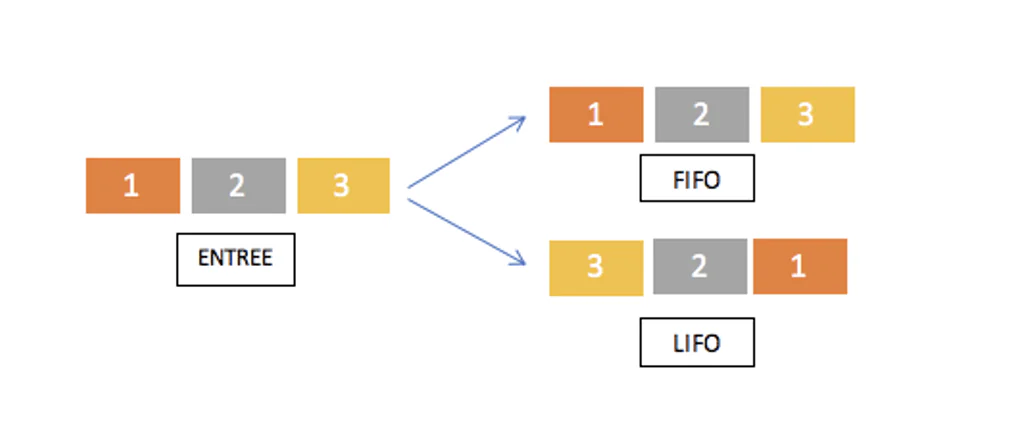
4. Man-Machine Efficiency:
Problem: Usually floor level employees are expected to dedicate shifts of more than 12 hours at a time, due to which they generally feel sleepy in the night shift and that affects the productivity of the organization. On the other hand, the machinery doesn’t get maintenance at regular intervals and causes breakdowns.
Solution: The efficiency of machinery and manpower is a must for the betterment of productivity in production. Preventive maintenance of machinery on regular intervals will avoid breakdowns certainly.
Bring in better employee engagement solutions for manpower efficiency like offering tea twice at night shift, providing a sufficient area for resting or taking a mini nap, and restarting the work can help improving the productivity.
5. Super Scheduling :
Problem: There is a big communication gap between the departments and the assignment of tasks. Companies habitually do not schedule tasks. The tendency is generally, as soon as production department receives the order from the sales team, they start producing and sending it to the dispatch department. After receiving the final goods, the dispatch department starts planning for dispatching.
Solution: Dispatching is something that has to be planned way in advance as it includes the loading-unloading process, and also the logistics are not available all the time, especially for a particular order to dispatch. If scheduling is defective, Dispatching is bound to be adversely affected in achieving the timely delivery. Track through the report and plan the things in advance.
Scheduling in the form of Bar chart makes your job easier as it provides a timetable for manufacturing and dispatching activities. It’s objective is to get the output within the cycle time and deliver the product in a definite time as you can see in the following example :
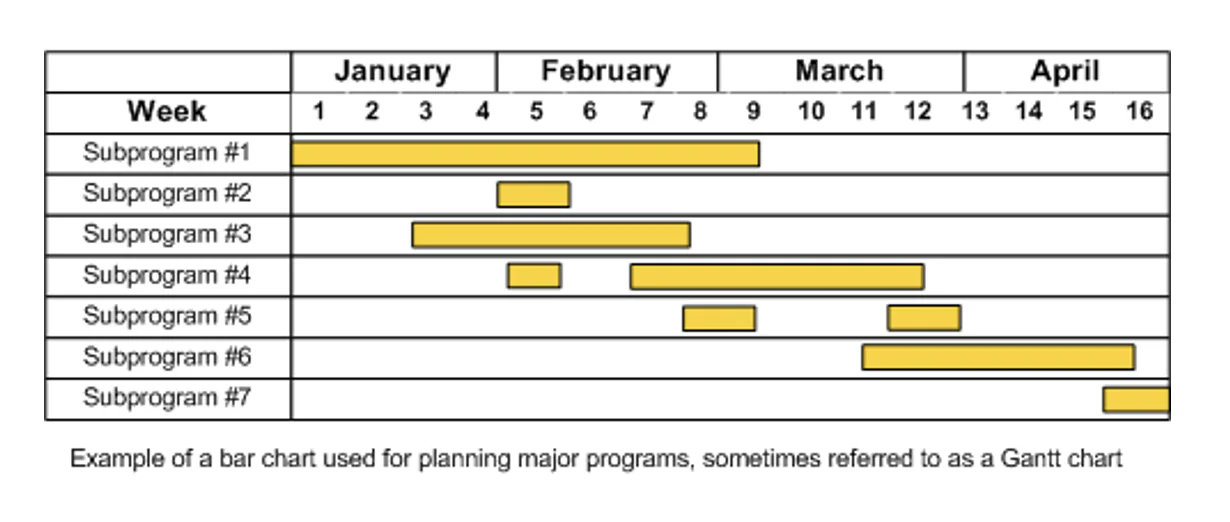
6. Check them for a “Cheque” :
Problem : Sometime quality check and analysis are not done properly, which leads to increase in rejections and returns. Also, detecting the reason of rejections becomes difficult.
Solution: Run a strong round of Inspection and Evaluation by effective QC Dept. It helps in maintaining the quality and evaluating the efficiency of processes so that improvement can be made to achieve standard performance and reduces rejections. It also reduces wastage and improve profitability with “First Time Right” (FTR) policy.
The Key Takeaway :
The numerous advantages of production planning and control demonstrate that it can boost a company’s revenues and reduce costs by maximizing the utilization of resources and minimizing wastage.
Well said by Benjamin Franklin,
You may “Delay” but Time will not.