In today’s competitive landscape, flawless execution is paramount. Customers demand high-quality products delivered promptly, and businesses strive for efficiency to remain profitable.
Enter the “First-Time Right” (FTR) concept, a powerful approach that empowers organizations to deliver consistently exceptional results.
FTR is a concept from Total Quality Management (TQM) that aims to ensure that activities are performed correctly the first time so that no rework is necessary. It’s a key part of Six Sigma, manufacturing consultant and companies often use it to track flawed products and redoing work.
The FTR guide for your Business Success
It is a philosophy ingrained in every step of a process, ensuring tasks are completed correctly from the outset.
Imagine a clothing manufacturer where every stitch sits perfectly on the first try – that’s the power of FTR. Being a manufacturer consultant, the FTR rate, expressed as a percentage, reflects this success:
FTR (%) = (Number of units produced without rework / Total number of units produced) x 100
Did You Know about These Multifaceted Benefits of FTR?
- Reduced Costs: Minimized rework translates to significant savings on materials, labor, and machine downtime (a PWC study suggests rework in manufacturing alone can cost 10-20% of production costs).
- Enhanced Customer Satisfaction: Flawless products build trust and loyalty, leading to repeat customers and a positive brand reputation.
- Improved Operational Efficiency: Fewer errors lead to smoother workflows, increased production output, and a higher “First Pass Ratio” (defect-free products).
FTR in Action: A Manufacturing Case Study
A real-world story: a charge air cooler manufacturer with an initial 85% final pass ratio, meaning 15% of products required rework due to inconsistencies. How they utilized FTR through a manufacturing consultancy like Stratefix?
Step 1: Define and Measure the Problem
The manufacturing consulting services helped them meticulously analyzed production and identified the specific issues hindering quality.
Step 2: Root Cause Analysis
A thorough analysis revealed a lack of control in maintaining critical parameters during setup, welding, testing, and painting.
Step 3: Improvement by Process Change
Customized fixtures and gauges were implemented to ensure continuous monitoring and prevent welded component distortion.
Step 4: The FTR Success
Following these changes, the first pass ratio skyrocketed to an impressive 94%, signifying a dramatic reduction in defects and rework, boosting productivity and reducing repair costs.
This case study beautifully illustrates the power of proactive FTR implementation. Identifying and addressing challenges led to significant success. Ongoing calibration by their Quality team ensures sustained effectiveness.
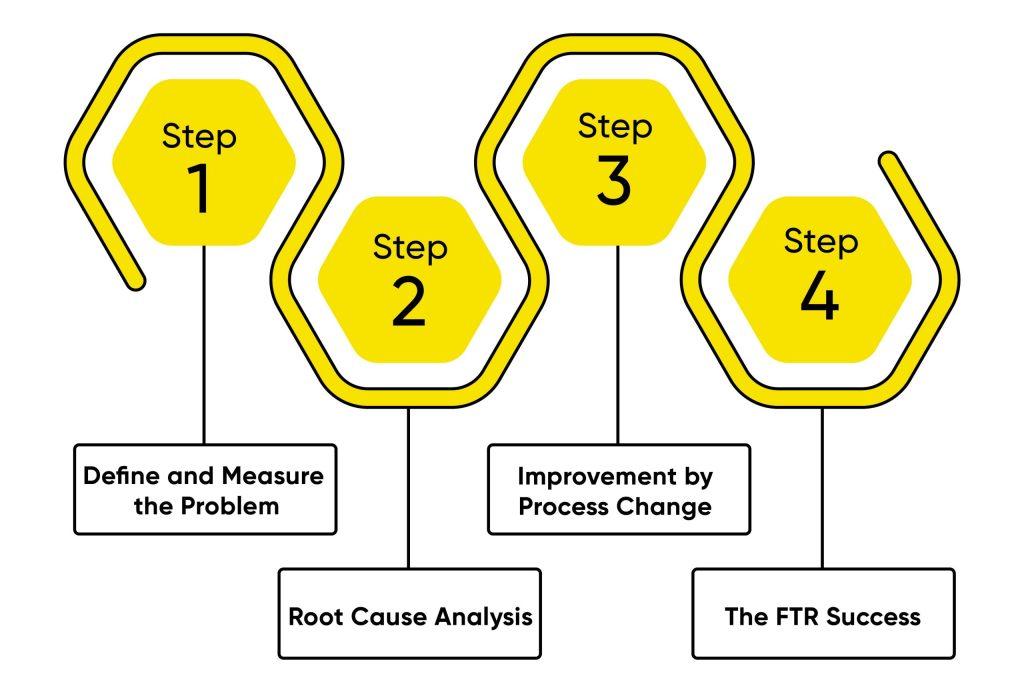
Being an operations management consultant, we recommend using Cutting-edge technologies like automation, Artificial Intelligence (AI), and predictive analytics which can further enhance FTR:
- Streamlined workflows: Precise robots and automated systems minimize human error.
- Real-time error identification: Continuous data monitoring allows for instant correction of process deviations, preventing defective products.
- Predictive maintenance: By analyzing sensor data, potential equipment failures can be predicted and addressed proactively.
In running any business – Proactive Control is The Key to Success!
Industry-Specific FTR Strategies You Can’t Afford to Miss!
Pharmaceuticals Industry:
- Implement stringent quality checks throughout production (e.g., X-ray scanners for foreign object detection).
- Utilize automated dispensing and filling systems to minimize medication errors (studies show dispensing errors account for nearly 50% of all medication errors [Institute for Safe Medication Practices]).
- Train staff on Good Manufacturing Practices (GMP) to ensure consistent product quality
(e.g., barcode scanning for correct medication selection). - Integrate real-time monitoring systems to track production parameters and identify potential deviations early.
- Invest in data analytics to analyze production data & identify areas for improvement in FTR (a McKinsey report highlights how big data analytics can reduce clinical trial times by up to 50%).
The Cost of Getting It Wrong: A real life Pharmaceutical Story
A reputed company experiencing high rates of defective inhalers due to misaligned valves.
This resulted in product recalls, production delays, and increased costs due to rework and wasted materials.
As an operations consulting firm, we always recommend FTR principles, including stricter quality checks and automated valve alignment systems, which in this case could have prevented these pitfalls.
Renewable Industry: A Solar Panel Installation and Green Energy Case Study
A solar energy company initially experienced high rework rates due to improper panel installation angles, leading to reduced energy output.
By adopting FTR practices including digital surveying tools, detailed checklists and comprehensive crew training, the company achieved a significant reduction in rework, leading to faster project completion times, improved efficiency, and enhanced customer satisfaction.
The global solar panel market is expected to reach a staggering $1.9 trillion by 2027 [Moneytalks], making FTR crucial for this industry.
Textile and Garment Manufacturing: A Stitch in Time Saves Nine (and Money!)
Let’s shift gears to our most recent story: Meet Priya, a passionate entrepreneur leading “Priya’s Panache,” a thriving textile and garment manufacturing unit in Surat, India.
Priya’s company specializes in exquisite silk sarees, known for their intricate designs and vibrant colors. However, a hidden gremlin lurked in their production process – inconsistencies.
Fabric defects, mismatched colors, and uneven stitching plagued their output, leading to:
- Frustrated Customers: Disappointed customers receiving flawed sarees resulted in negative reviews and lost business.
- Wasted Resources: Spoiled fabric and rework loops meant wasted money on raw materials and labor.
- Demoralized Workforce: The constant pressure to rectify errors impacted employee morale.
Priya, determined to elevate her brand, discovered the magic of FTR. Partnering with Stratefix Consulting.
Priya implemented several key changes such as RFT, yet another key KPI in garment manufacturing, alongside DHU, to ensure quality production.
By measuring RFT, the factory gauged the quality of its process:
- Investing in Automation: Priya replaced manual fabric cutting with laser cutting machines, minimizing fabric wastage (a National Institute of Industrial Engineering study suggests fabric wastage in the Indian garment industry can be as high as 15-20%).
- Quality Control Checkpoints: Meticulous quality checks were integrated throughout production, ensuring timely defect identification and rectification.
- Digital Color Matching: Priya invested in digital color matching technology to ensure consistent and vibrant hues in the finished sarees.
- Employee Training: The team received comprehensive training on advanced weaving and stitching techniques, empowering them to create flawless garments.
The results were truly transformative. Priya’s Panache achieved a significant increase in their FTR rate, leading to:
- Flying Customer Satisfaction: Flawless sarees delivered on time brought smiles to customer’s faces with positive word-of-mouth promotion.
- Reduced Costs: Minimized rework and wastage led to significant cost savings, allowing Priya to invest in further growth.
- Empowered Workforce: The team took pride in their ability to produce high-quality garments, boosting morale and productivity.
Priya’s story exemplifies the transformative power of FTR in the textile and garment industry, a sector that employs over 45 million people in India alone (Invest India)!
This blog is Part 1 of a 2-part series. Stay tuned for Part 2 where we will explore the DMAIC methodology, a cornerstone of Lean Six Sigma, which provides a structured approach to implementing and sustaining FTR!
FTR: Your Partner in Growth alongside Stratefix!
The above stories of Business owners illustrate the transformative power of FTR across various industries. By prioritizing getting it right the first time, businesses can achieve:
- Reduced Costs: Minimized rework, waste, and errors lead to significant cost savings.
- Enhanced Customer Satisfaction: Flawless products and services build trust and loyalty.
- Improved Efficiency: Streamlined workflows and fewer errors boost productivity and profitability.
- Stronger Brand Reputation: A commitment to quality elevates your brand image.
Stratefix Consulting: Your Guide to FTR Excellence
The road to FTR excellence can be challenging. Stratefix Consulting, with over 65 industries under our belt, is your trusted partner. We offer a comprehensive approach to FTR implementation, including:
- Identifying Hidden Gaps: We analyze your operations to pinpoint areas for improvement.
- Data-Driven Strategies: We leverage data analytics to identify root causes and measure FTR progress.
- Customized Solutions: We develop FTR plans tailored to your specific industry and needs.
- Implementation Support: We actively guide you through the entire FTR implementation process.
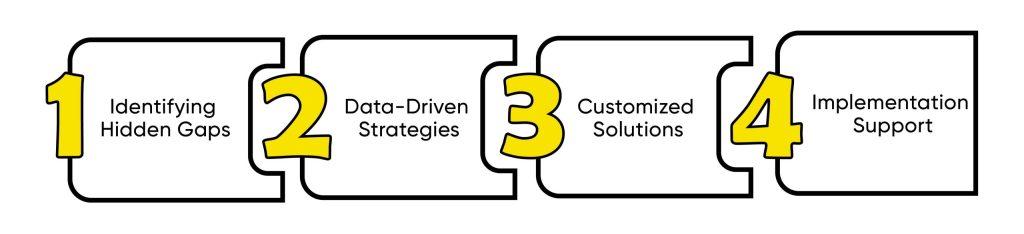
Embrace FTR and Revolutionize Your Business Operation
Don’t wait! Contact Stratefix Consulting today and unlock the transformative power of FTR.