In today’s fast-paced retail landscape, efficient inventory management is essential for minimizing losses, reducing operational costs, and ensuring smooth day-to-day operations.
A leading store encountered significant challenges with its existing inventory system, including unutilized space, stock mismatches, and inefficient product placement.
To address these issues, the textile manufacturer partnered with Stratefix Consulting to optimize its inventory setup, streamline workflows, and boost storage efficiency.
Through a comprehensive analysis of the store’s layout and inventory management practices, Stratefix Consulting identified key inefficiencies in space utilization, product placement, and tracking.
The proposed solutions involved reorganizing the store layout, introducing a rack identification system, and implementing a bin mapping strategy to reduce inventory handling time and costs.
This case study delves into the store’s transformation and highlights the quantifiable improvements resulting from Stratefix’s inventory management solutions.
Check out the below images and you will see how unorganized and misplaced the inventories were across all department floors:
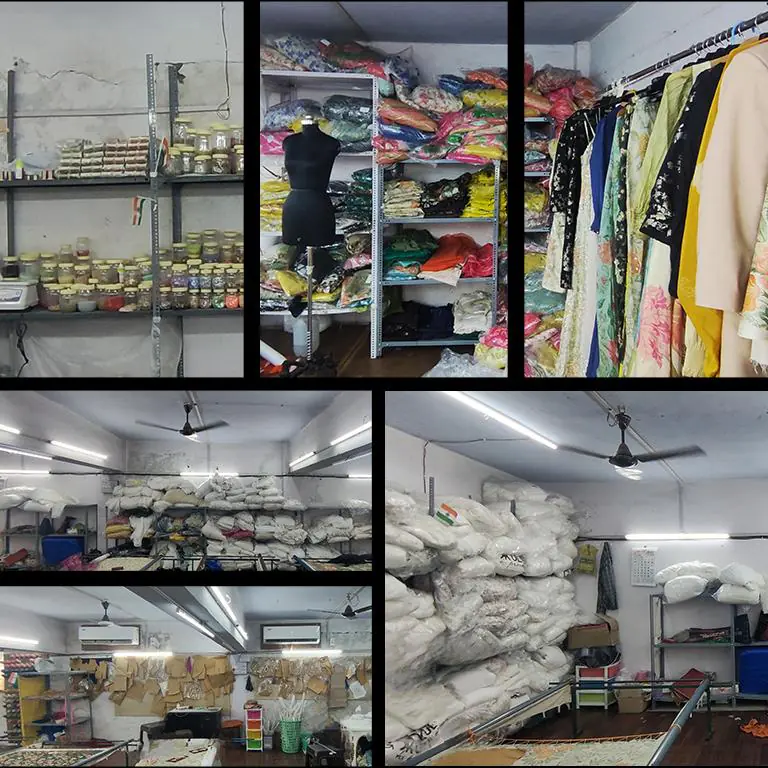
Key Challenges Identified as shown in the above images
1. Unutilized and Overloaded Storage Space
The store’s existing storage racks were underutilized, with significant portions of the space left empty or improperly organized. Overloading certain areas with excess stock, particularly fabric, led to inefficient space management, while other parts of the store remained underused .
Impact: Inefficient use of space led to clutter, making it difficult for employees to locate items quickly. This resulted in increased time spent on inventory handling, higher labor costs, and delays in customer fulfilment.
2. Unorganized Product Layout and Stock Mismatch
The scattered and unorganized placement of inventory items further complicated the situation. Products such as zari lace, stones, and spare parts were not stored systematically, leading to stock mismatches and loss of inventory .
Impact: The lack of a structured layout meant frequent errors in stock counts, increasing the likelihood of overstocking or understocking certain items. This not only raised operational costs but also impacted the store’s ability to manage stock levels effectively.
3. Excessive Time Spent on Locating Goods
Due to the unorganized layout, employees were spending excessive time locating items. The absence of a clear system for tracking products’ exact locations in the store exacerbated this problem .
Impact: Increased time spent searching for goods directly impacted productivity and customer satisfaction. Delays in order fulfilment due to stock retrieval issues were common, further increasing operational inefficiencies.
After carefully analysing the entire process, from designing to delivering the final product, Stratefix’s Operation team suggested several inventory management system based on space, inventory and keeping all other requirements intact. Check out the examples in below images:
Stratefix Consulting’s Approach in Inventory management in textile and apparel industry
To tackle these challenges, Stratefix Consulting proposed a range of solutions that involved reorganizing the store’s physical layout, implementing a structured inventory system, and utilizing modern tools for tracking and monitoring inventory levels. Below images are a few examples.
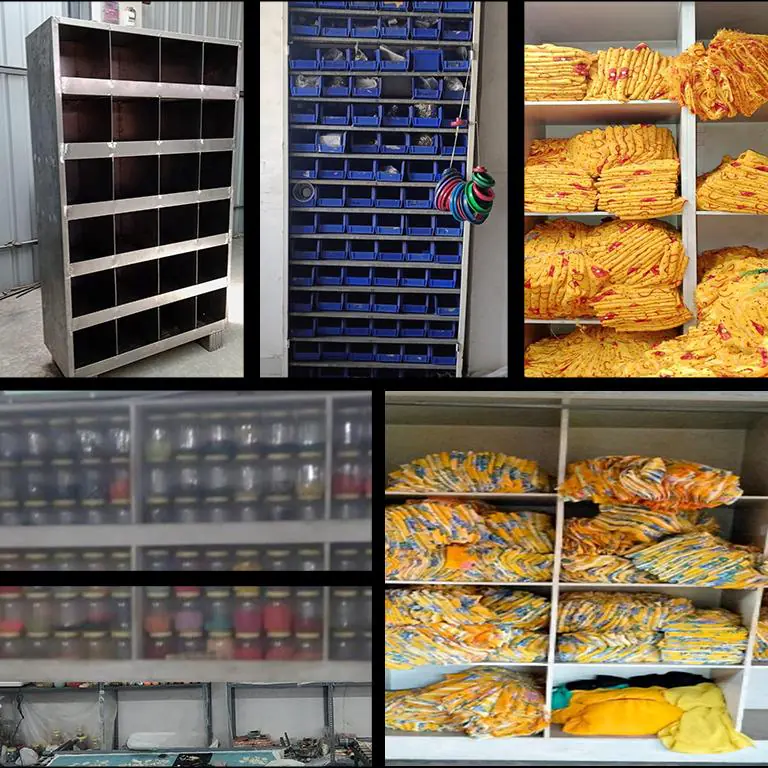
1. Optimizing Space Utilization with Rack Columns
Stratefix proposed the installation of additional rack columns in the form of pigeon racks, maximizing the vertical space available in the store. These pigeon racks allowed for more organized storage of small but valuable raw materials such as zari lace and stones .
Solution: By increasing the number of rack columns and mapping products to specific bins, the store could make better use of its available space. Each product was assigned a designated bin location, ensuring easy access and reducing clutter.
Result: Space utilization increased by 40%, allowing the store to store more inventory in the same footprint while maintaining easy access to all items.
2. Introducing a Rack Identification System
A structured rack identification system was introduced to map goods to their respective racks, with each item tagged and assigned a bin location. This system ensured that employees could locate products quickly and efficiently, reducing search times.
Solution: The rack identification system was integrated with an inventory tracking tool, where each product was assigned a material code and its location was automatically displayed and highlighted in the system or Excel.
Result: Goods retrieval times were reduced by 50%, improving workflow efficiency and speeding up order fulfilment. The store also experienced fewer stock mismatches and inventory losses due to improved tracking.
3. Continuous Monitoring and Systematized Inventory Tracking
Stratefix developed an inventory tracking module in Excel, allowing the store to maintain up-to-date records of stock levels, product locations, and bin assignments. Continuous monitoring of inventory was implemented to ensure data accuracy and reduce handling costs .
Solution: The system was designed to provide real-time updates on stock levels, with alerts for low stock and automatic generation of replenishment orders when required.
Result: Inventory management costs decreased by 35% as a result of reduced labor hours and minimized errors in stock counts. The store also reported fewer incidents of stockouts and overstocking, leading to better cash flow management.
Results and Key Performance Metrics
Stratefix’s approach to inventory optimization delivered significant improvements across several key metrics. This uniquely designed process of Inventory management in the textile and clothing industry led to overseeing and controlling the flow of goods from their manufacturing units to retail outlets or directly to walk-in customers:
- Space Utilization: The introduction of additional rack columns and the reorganization of storage space increased space efficiency by 40%, allowing the store to store more items without expanding its physical footprint.
- Time Savings: Employees spent 50% less time retrieving items due to the structured rack identification and bin mapping system. This translated into faster order fulfilment and improved productivity.
- Inventory Accuracy: Stock mismatches were reduced by 25%, leading to better accuracy in stock counts and fewer instances of lost or misplaced inventory.
- Cost Reduction: Inventory handling costs decreased by 35%, primarily due to reduced labour hours and improved tracking accuracy. The structured system also helped minimize the risk of inventory losses.
- Operational Efficiency: By streamlining the inventory management process, the store saw a 25% improvement in overall operational efficiency. The implementation of real-time inventory tracking allowed the store to make data-driven decisions regarding stock replenishment and storage optimization.
Conclusion
Inventory management in the fashion and retail industry helps minimise fashion risk by closely monitoring sales performance and adjusting inventory levels accordingly. We implemented an Inventory management software exclusive for the apparel industry which tracks clothing, shoes, jewellery, accessories and related items as they move between locations.
Stratefix Consulting’s strategic approach to optimizing the store’s inventory management system yielded impressive results, transforming the store’s operations and positioning it for long-term success.
By addressing inefficiencies in space utilization, product placement, and inventory tracking, Stratefix enabled the store to significantly reduce costs, improve productivity, and enhance customer satisfaction.
This case study highlights the importance of effective inventory management in a retail environment, demonstrating how simple yet impactful changes can drive operational excellence and support business growth.
As the store continues to benefit from these improvements, Stratefix remains committed to providing ongoing support and monitoring to ensure that the store’s inventory management system continues to evolve with its needs.
If you’re facing inventory management challenges in industries such as Textiles, FMCG, Retail, Pharmaceuticals, Luxury Goods and Jewelry, Heavy Engineering, or Apparel and Fashion, Stratefix Consulting’s core operational experts are here to help.
Our tailored solutions address every aspect of inventory optimization, from space utilization to real-time stock tracking and bin mapping systems, ensuring efficiency and cost reduction at every stage.
Whether you need to minimize stock mismatches, reduce handling costs, or improve overall workflow, we apply industry-specific strategies designed to meet your unique needs.
Don’t wait until inefficiencies erode your profitability—partner with Stratefix Consulting today to implement a data-driven inventory management system that aligns with your business goals.
Reach out now to experience measurable improvements in operational efficiency, cost savings, and inventory accuracy in as little as a few weeks. Let’s transform your business operations for the better.
Contact us today to find out how we can help you achieve excellence.